A saber-making machine typically refers to a specialized machine used in the production of sabers or similar types of curved blades, often used for ceremonial, martial arts, or historical reproduction purposes. While there may not be as many machines specifically marketed under this name, the process generally involves several stages, including forging, shaping, and finishing. Here’s an overview of relevant features, processes, and applications:
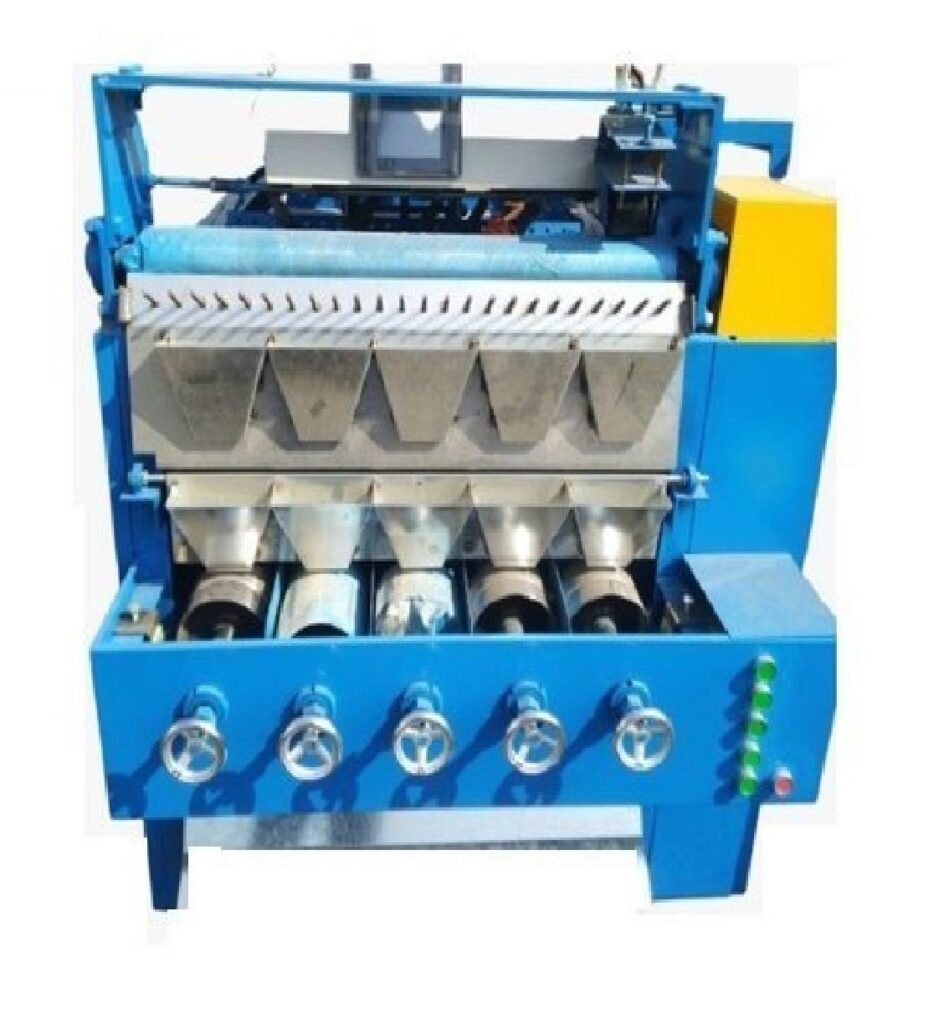
Key Features
Forging Mechanism:
- The machine often incorporates a forge that heats metal to make it malleable for shaping.
- Hydraulic or mechanical presses are commonly used to shape the blade from heated metal.
Shaping and Grinding:
- After forging, the blade is shaped and refined using various grinding wheels and tools to achieve the desired curvature and sharpness.
Heat Treatment:
- This process involves hardening and tempering the blade to improve its strength and durability.
- It may include controlled heating and cooling processes.
Finishing:
- Machines may also include polishing and coating stations to enhance the appearance and protect the blade from corrosion.
Types of Machines
Hammer Forging Machines:
- Used for shaping metal by applying force through repeated blows.
CNC Machines:
- Computer Numerical Control (CNC) machines can automate the shaping and grinding processes, allowing for precise control over dimensions and designs.
Belt Sanders and Grinders:
- Used for finishing the blade edges and surfaces, ensuring smoothness and sharpness.
Applications
- Martial Arts: Manufacturing sabers for practices in disciplines like Kendo or Filipino martial arts.
- Reproductions: Creating historically accurate replicas for collectors and museums.
- Ceremonial Use: Producing decorative sabers for military or ceremonial purposes.
Advantages
- Precision: Modern machines, especially CNC units, allow for highly precise cuts and shapes, resulting in consistent quality.
- Efficiency: Automating parts of the process can speed up production while maintaining quality.
- Customization: Many machines allow for various designs, making it possible to create unique pieces.
Maintenance
Regular maintenance is crucial for optimal performance, which may include:
- Cleaning and lubricating moving parts to prevent wear.
- Regularly inspecting and sharpening tools and blades.
- Ensuring safety features are functioning correctly.