A hydraulic plate machine, often referred to as a hydraulic press brake or hydraulic bending machine, is a type of industrial equipment used for bending and shaping metal sheets or plates. Here are some key points about it:
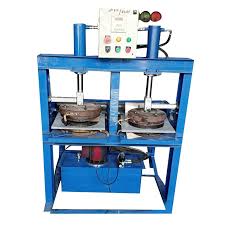
Working Principle
- Hydraulic System: It operates using hydraulic power, which allows for high force applications with minimal manual effort. The hydraulic system utilizes fluid pressure to move a ram, which bends the material.
- Die and Punch: The machine typically consists of a stationary lower die and a moving upper punch. The metal sheet is placed between them, and when the punch descends, it deforms the material into the desired shape.
Features
- Precision Control: Many hydraulic plate machines have advanced controls for precision bending, allowing for accurate angles and dimensions.
- Adjustable Stroke: The stroke length can often be adjusted to accommodate various material thicknesses and bending requirements.
- Safety Features: Modern machines come with safety measures to protect operators, such as emergency stop buttons and protective enclosures.
Applications
- Sheet Metal Fabrication: Commonly used in industries like automotive, aerospace, and manufacturing for fabricating parts.
- Custom Bending: Ideal for producing complex shapes and designs, including brackets, panels, and frames.
Advantages
- Versatility: Can handle a wide range of materials and thicknesses.
- High Force Capacity: Capable of bending thick plates that require substantial force.
- Reduced Operator Fatigue: Hydraulic operation reduces the physical strain on operators compared to manual machines.
Maintenance
Regular maintenance is crucial for optimal performance and longevity, including checking hydraulic fluid levels, inspecting seals and hoses, and ensuring all mechanical components are in good working order.