A water pouch packing machine is designed for filling and sealing pouches or bags with water, typically for commercial distribution. These machines are commonly used in the beverage industry, especially for packaging purified water in pouches that are easy to transport and consume. Here are some key features and details:
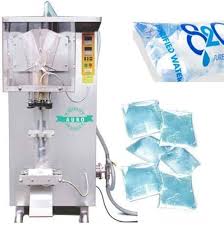
Key Features
Filling Mechanism:
- Uses either gravity, pressure, or vacuum filling methods to accurately dispense the right amount of water into each pouch.
- Can handle various pouch sizes depending on the machine design.
Sealing Technology:
- Employs heat sealing, ultrasonic sealing, or other sealing methods to ensure the pouches are securely closed and leak-proof.
- Some machines offer adjustable sealing temperatures and times for different materials.
Automation:
- Many machines are fully automated, incorporating features such as automatic pouch feeding, filling, sealing, and cutting, which enhances efficiency and reduces labor costs.
- Equipped with sensors to ensure proper positioning and filling.
Material Compatibility:
- Designed to work with various pouch materials, often including plastic films that are food-grade and suitable for liquid storage.
Applications
- Beverage Industry: Widely used for packaging purified or mineral water, especially in regions with limited access to bottled water.
- Food Service: Useful in catering and event services where water pouches can be distributed easily.
Advantages
- Cost-Effective: Pouch packaging is generally cheaper than traditional bottled packaging, both in terms of materials and transportation.
- Lightweight and Portable: Water pouches are easier to carry and distribute compared to glass or plastic bottles.
- Space Efficient: Pouches take up less space, making them easier to store and transport.
Maintenance
To ensure optimal performance, regular maintenance should include:
- Cleaning the filling nozzles and sealing components to prevent contamination.
- Checking for wear and tear on mechanical parts and seals.
- Regularly inspecting and calibrating filling volumes for accuracy.